Plastic extrusion for heat-sensitive plastics, PVC, and high-performance materials
Plastic extrusion for heat-sensitive plastics, PVC, and high-performance materials
Blog Article
Comprehending the Fundamentals and Applications of Plastic Extrusion in Modern Production
In the realm of modern-day manufacturing, the technique of plastic extrusion plays a crucial role. Unraveling the principles of this process exposes the true versatility and potential of plastic extrusion.
The Fundamentals of Plastic Extrusion Process
While it may show up complex, the basics of the plastic extrusion process are based upon relatively straightforward concepts. It is a production procedure wherein plastic is melted and after that formed right into a continual account through a die. The raw plastic product, typically in the type of pellets, is fed into an extruder. Inside the extruder, the plastic undergoes warmth and pressure, creating it to thaw. The liquified plastic is then compelled through a designed opening, called a die, to develop a long, continuous product. The extruded item is cooled down and afterwards cut to the desired size. The plastic extrusion process is extensively utilized in different sectors due to its cost-effectiveness, versatility, and efficiency.
Various Types of Plastic Extrusion Methods
Structure upon the fundamental understanding of the plastic extrusion procedure, it is required to check out the numerous strategies entailed in this manufacturing technique. In comparison, sheet extrusion develops large, level sheets of plastic, which are typically more refined into items such as food packaging, shower drapes, and car parts. Recognizing these strategies is crucial to utilizing plastic extrusion efficiently in modern manufacturing.
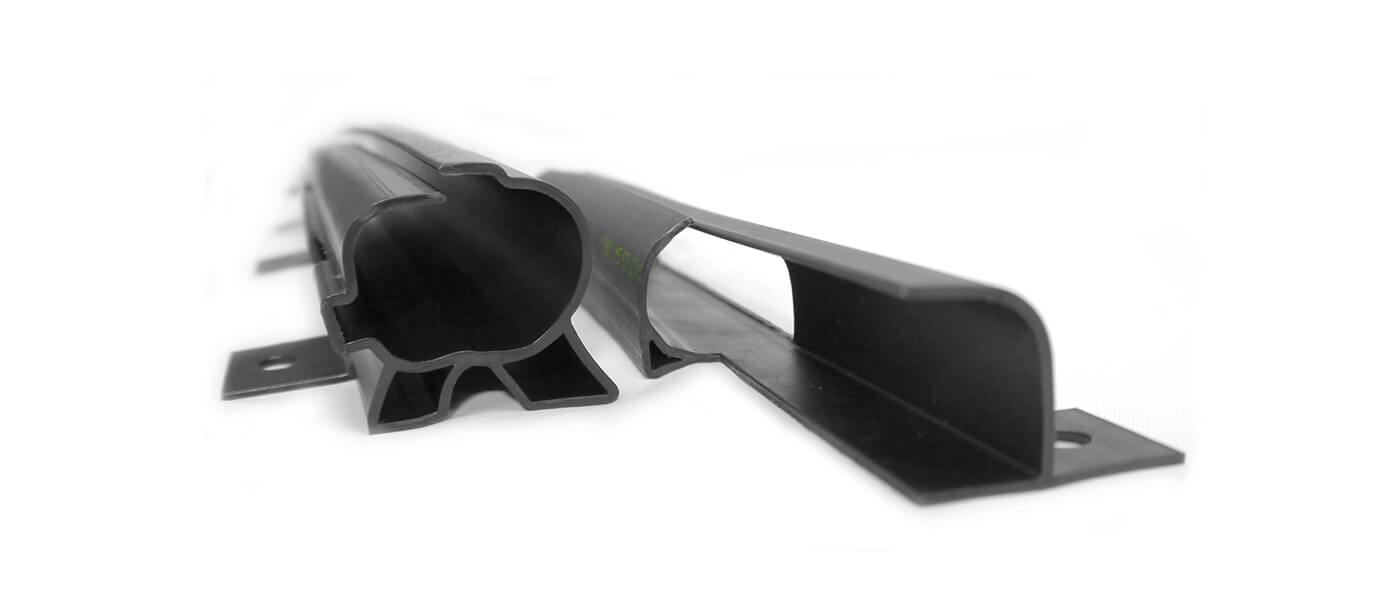
The Function of Plastic Extrusion in the Automotive Sector
A frustrating majority of parts in modern-day automobiles are items of the plastic extrusion procedure. This process has actually revolutionized the vehicle market, changing it into a much more reliable, affordable, and flexible manufacturing field. Plastic extrusion is largely used in the manufacturing of numerous car components such as check my reference bumpers, grills, door panels, and control panel trim. The process gives an uniform, regular result, enabling makers to create high-volume get rid why not look here of great precision and minimal waste. The lightness of the extruded plastic components adds to the general reduction in automobile weight, enhancing gas efficiency. Moreover, the resilience and resistance of these components to heat, cool, and impact enhance the durability of autos. Thus, plastic extrusion plays a crucial function in automotive manufacturing.
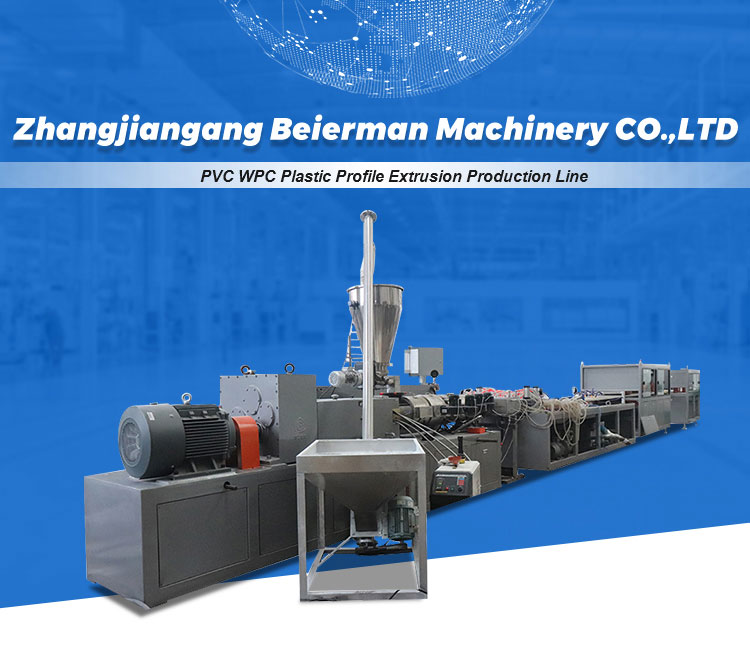
Applications of Plastic Extrusion in Consumer Item Manufacturing
Past its substantial effect on the auto market, plastic extrusion proves equally effective in the realm of customer items making. The versatility of plastic extrusion permits makers to create and generate complicated forms and sizes with high precision and performance. The versatility, versatility, and cost-effectiveness of plastic extrusion make it a favored option for several customer items suppliers, adding significantly to the sector's development and advancement.
Environmental Effect and Sustainability in Plastic Extrusion
The prevalent use of plastic extrusion in producing welcomes analysis of its eco-friendly ramifications. As a procedure that regularly utilizes non-biodegradable products, the ecological impact can be substantial. Power intake, waste production, and carbon discharges are all concerns. However, industry developments are enhancing sustainability. Effective machinery reduces power use, while waste administration systems reuse scrap plastic, lowering resources demands. In addition, the growth of biodegradable plastics offers a more ecologically friendly option. Despite these renovations, additionally innovation is required to minimize the environmental footprint of plastic extrusion. As society leans in the direction of sustainability, producers have to adapt to stay practical, emphasizing the value of continual research and advancement in this field.
Conclusion
In final thought, plastic extrusion plays a crucial duty about his in modern-day manufacturing, specifically in the auto and customer items fields. Recognizing the fundamentals of this procedure is crucial to maximizing its applications and advantages.
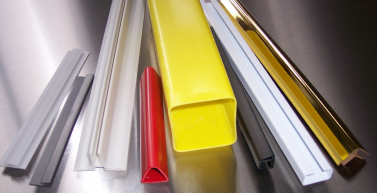
The plastic extrusion procedure is extensively made use of in various industries due to its efficiency, adaptability, and cost-effectiveness.
Structure upon the fundamental understanding of the plastic extrusion procedure, it is necessary to check out the various methods entailed in this production approach. plastic extrusion. In contrast, sheet extrusion creates huge, level sheets of plastic, which are typically more refined into products such as food packaging, shower drapes, and cars and truck parts.A frustrating majority of parts in modern-day lorries are products of the plastic extrusion procedure
Report this page